📢 OpenPhase News
Advanced Microstructure Simulation Suite
Empowering researchers and scientists with cutting-edge simulation tools for metallic materials, ceramics, and minerals. Experience the future of materials science.
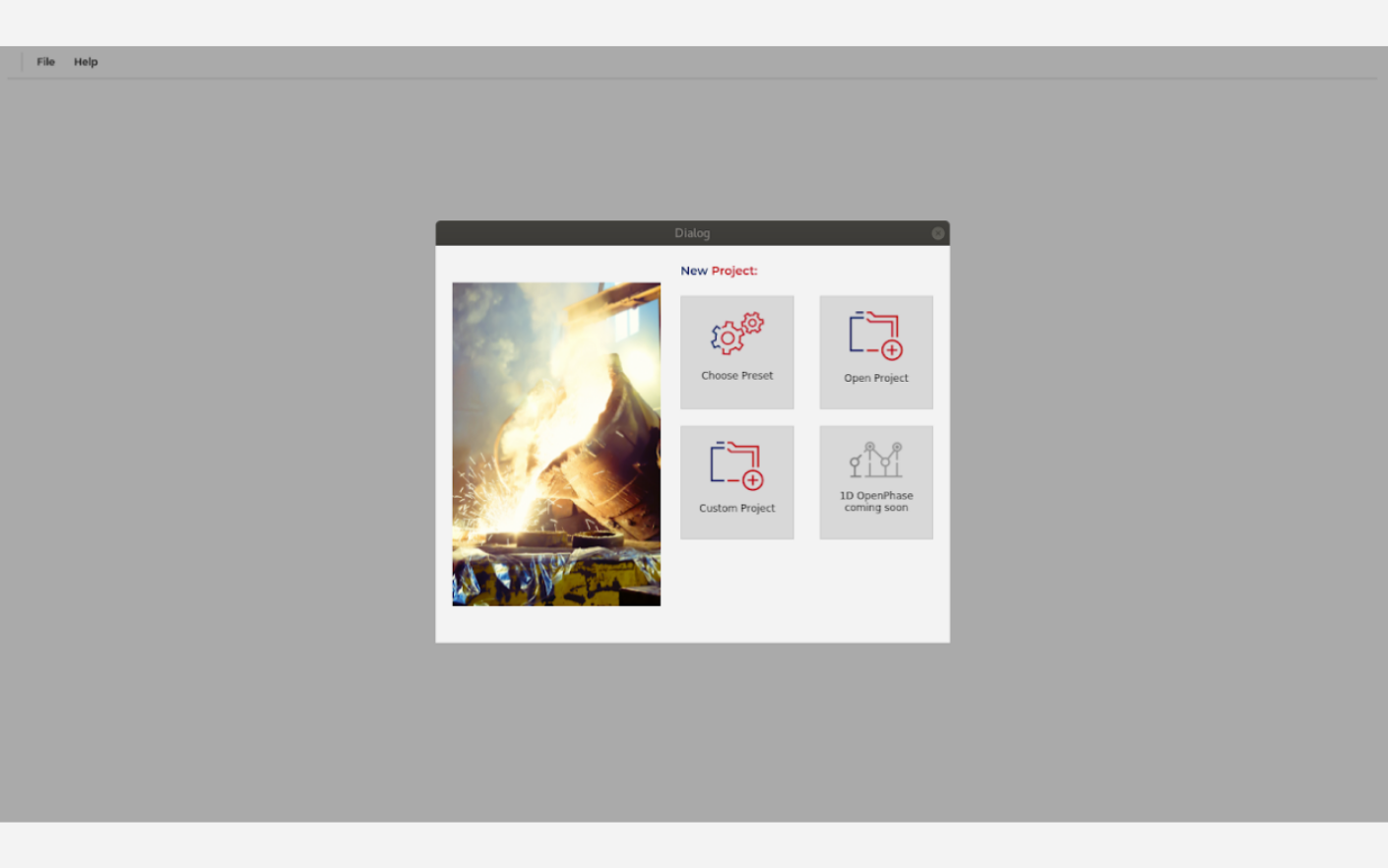
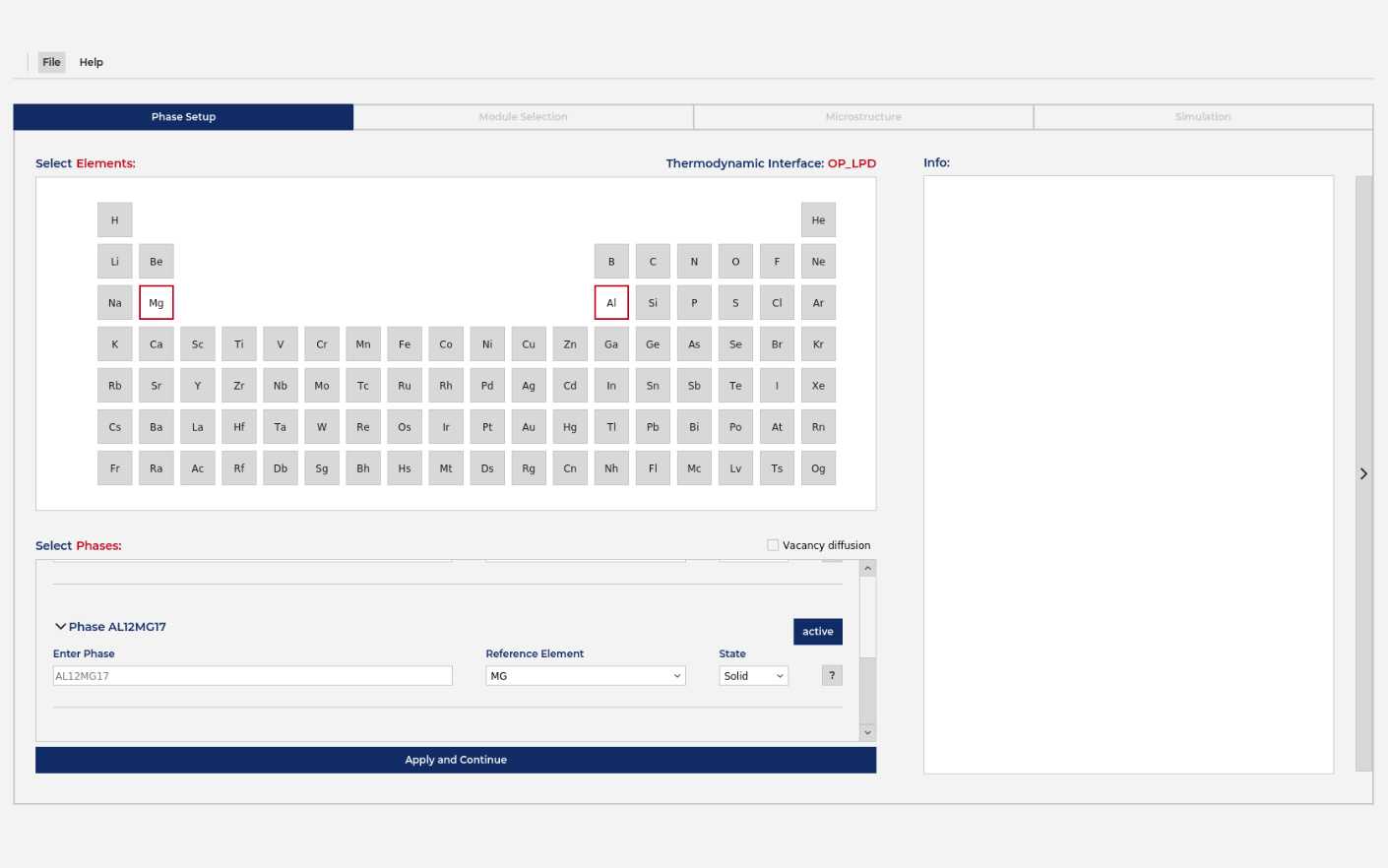
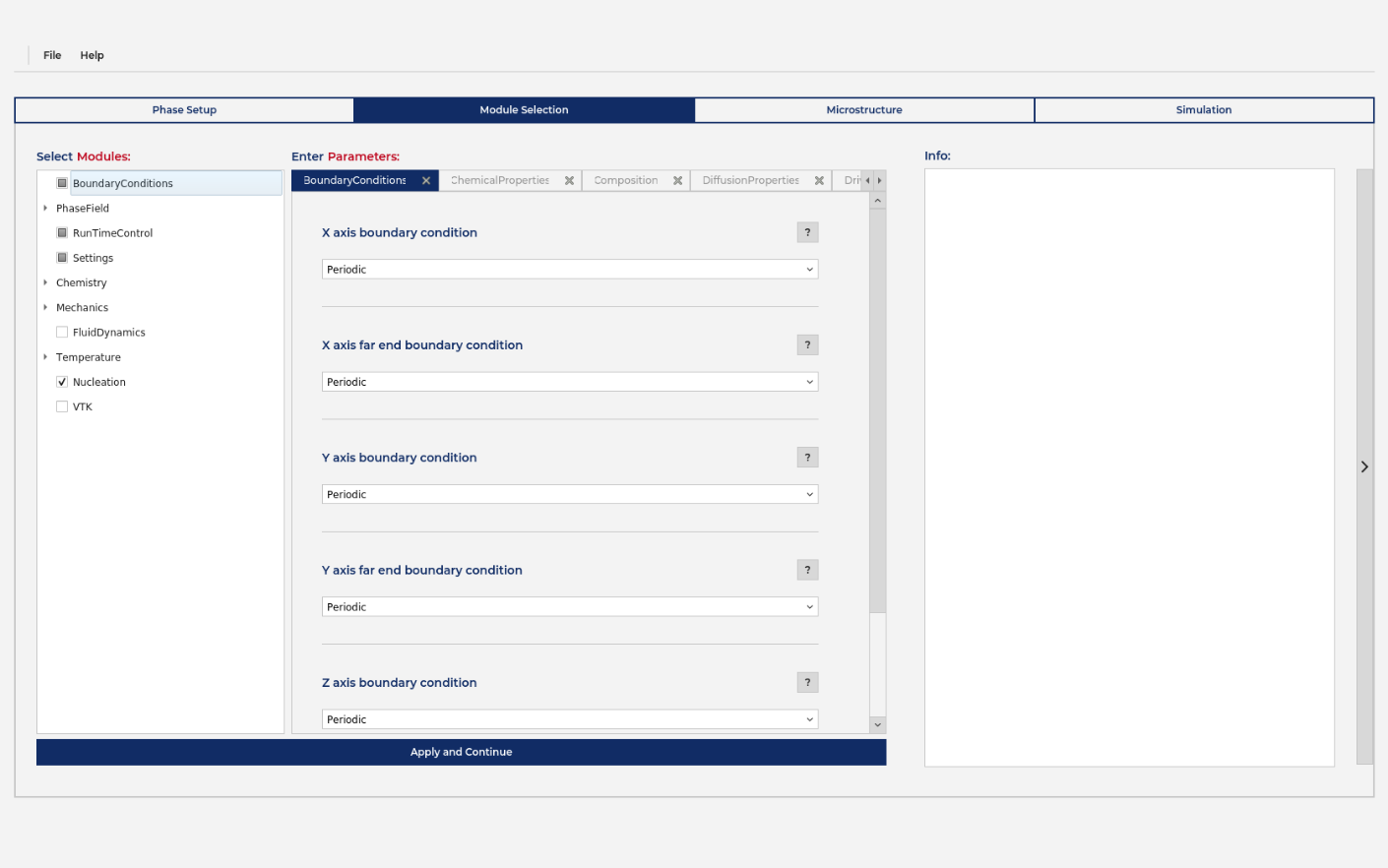
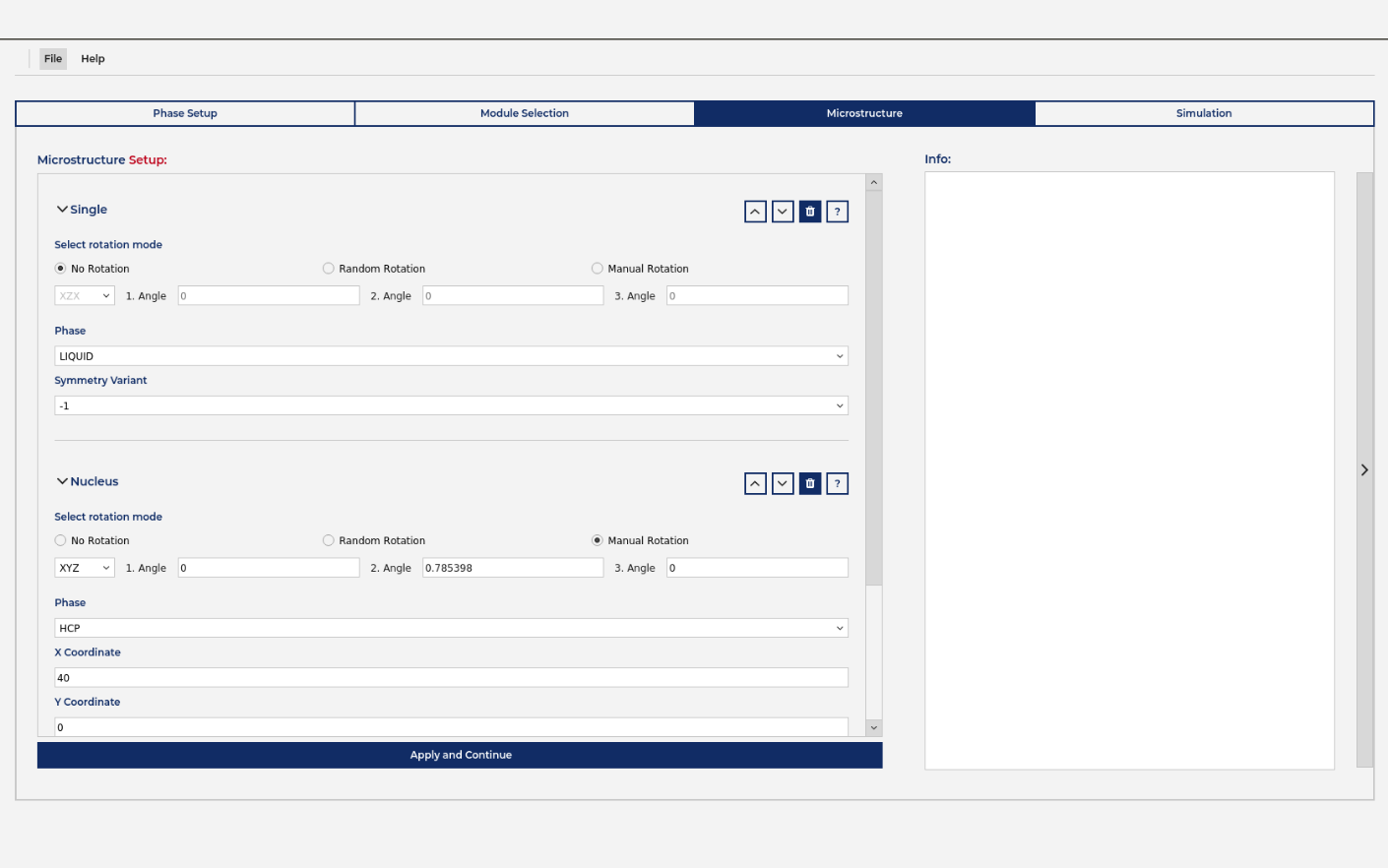
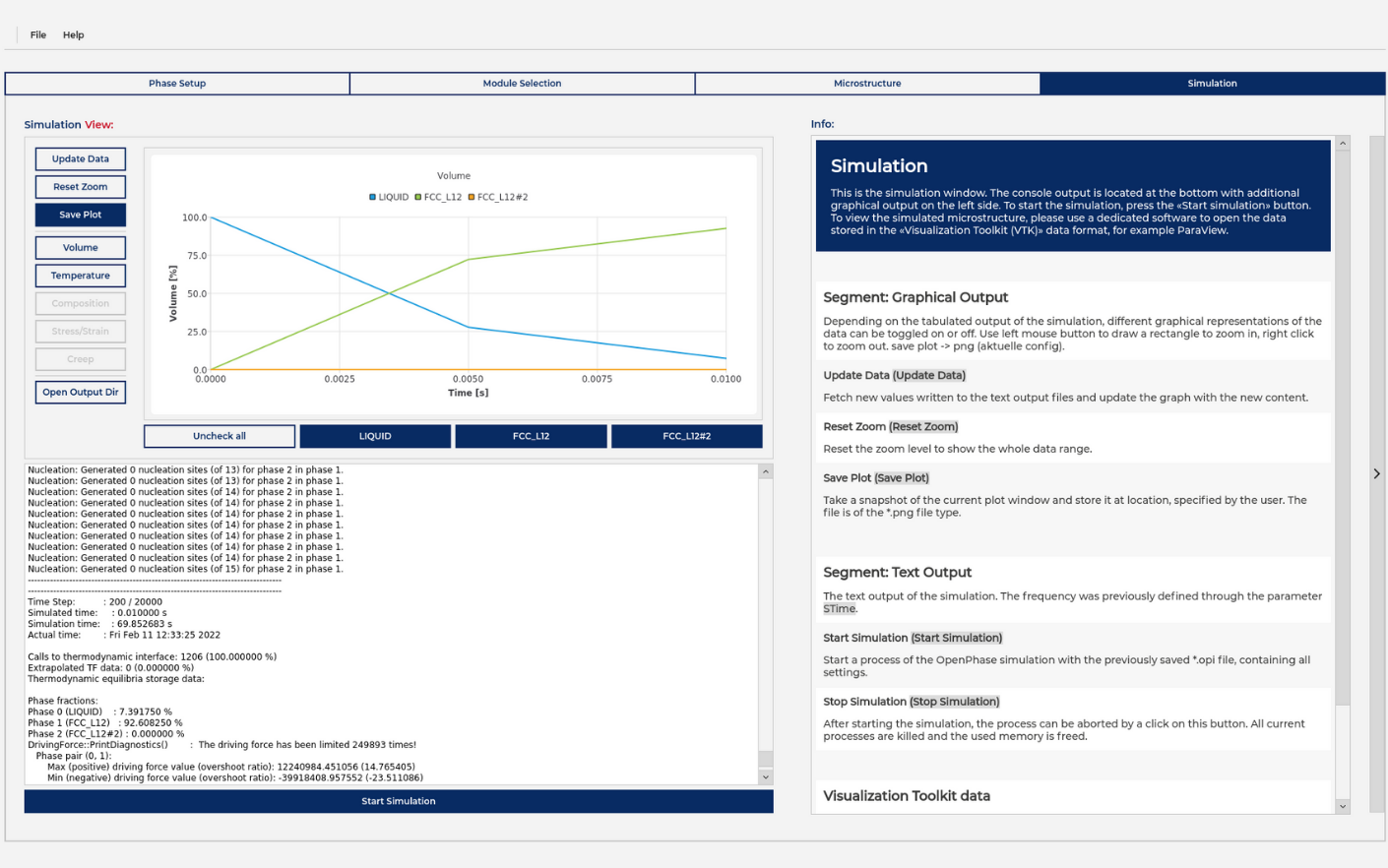
OpenPhase Software
OpenPhase Studio is a powerful microstructure simulation suite made for metallic materials, ceramics and minerals. Using multi-physics models embedded in the phase-field method, materials processes such as solidification, heat treatment, mechanical testing and many more can be simulated. OpenPhase is available in two flavours, OpenPhase Studio and OpenPhase Core. OpenPhase Studio is our full-featured microstructure simulation suite with user-friendly GUI, intuitive simulation setup and on-the-fly data analysis. An open-source C++ library is available with OpenPhase Core, which includes the core OpenPhase functionality and offers full flexibility in building custom simulations.
OpenPhase enables you to:
- Innovate and accelerate materials development
- Complement experiments
- Optimize processes through better understanding of materials behavior
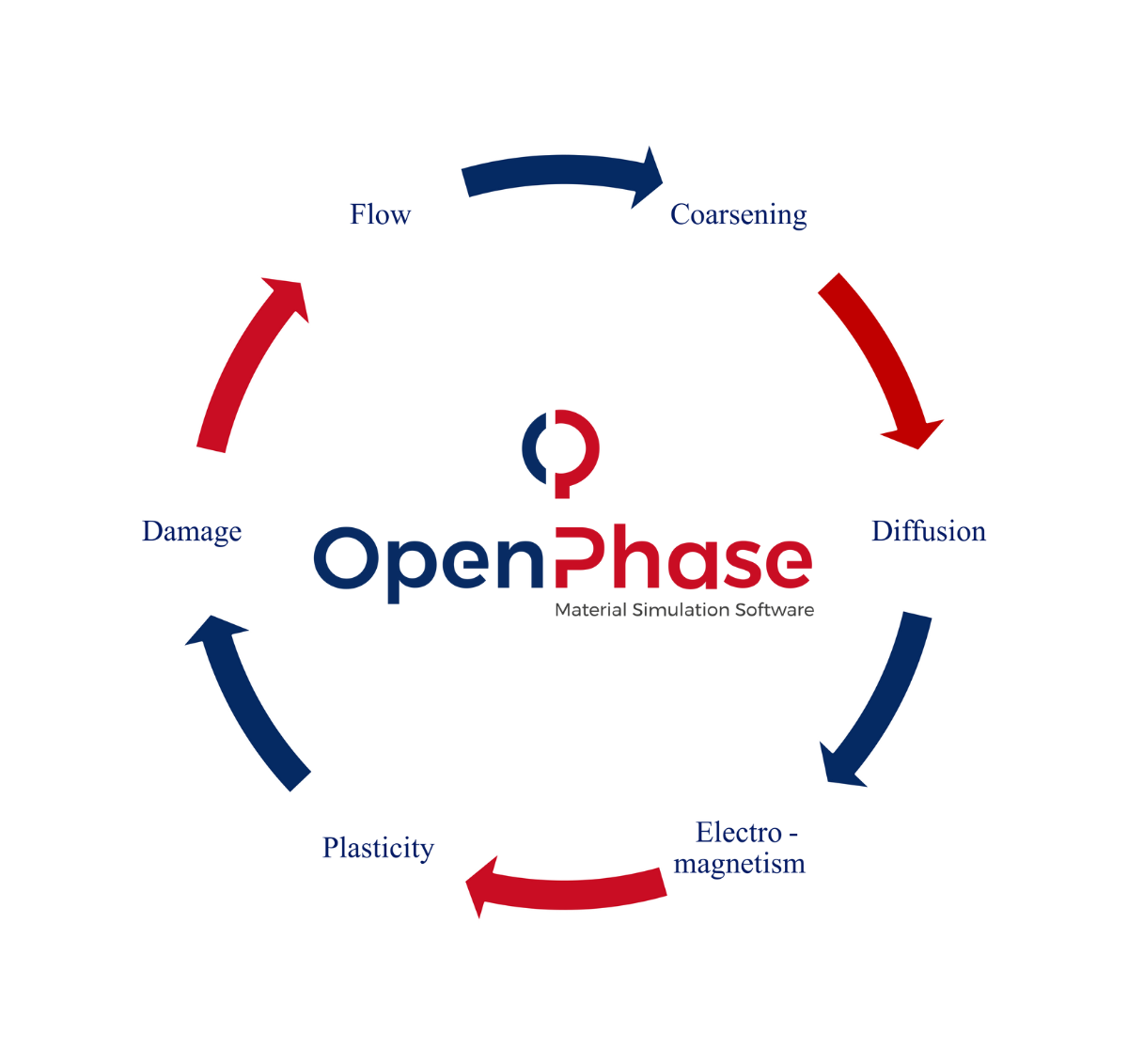
Advanced Research & Simulation Tools
Empowering scientific research with state-of-the-art phase-field simulation tools developed through decades of academic excellence
OPStudio
The Innovative Microstructure Simulation Suite
- Full-featured microstructure simulation suite with an intuitive GUI
- New simulations can be quickly created from pre-defined material and process presets
- Access to the source code for full insight and customization
- Includes an intuitive builder for new executables
- Compatible with commercial software like Abaqus, Thermo-Calc and our own products OPMech, OPDiff
- General features: MPI parallelism, OpenMP parallelism, Linux and Windows versions, Source control on request.
OPDiff
Revolutionize Your Multicomponent Alloy Simulation
- Extension to multicomponent alloy transformation and multicomponent diffusion
- Interface to the TQ-interface of Thermo-Calc
- Currently restricted to the quasi-equilibrium approach in pairwise extrapolation
- Finite-interface dissipation and grand potential applications will be available in near future
OPMech
Empower your simulations with advanced mechanics capabilities
- Extension to finite strain elasticity and phenomenological/dislocation-based crystal plasticity (FCCand BCC/BCT)
- Other symmetry classes available on request
- Large strain with adaptive remeshing will be available in near future
OPCustomSolutions
Unlock the full potential of your research with tailored simulations and custom solutions.
- Collaborate with our team of experts to achieve your specific goals
- Implement cutting-edge models, conduct comprehensive parameter studies, or develop customized interfaces
- Expertise and experience to tackle projects of any size and complexity
OPSupport
Your Trusted Partner in Material Modeling and Simulation
- Answers technical and scientific questions
- Helps you quickly find the right simulation setup for your material and process parameters
- Elevate your material modeling and simulation capabilities by partnering with OPSupport
OpenPhase Features
The development of OpenPhase started in 2008 at ICAMS, one of the world-leading materials simulation institutes. With today over 50 man-years of development, OpenPhase is the most feature-rich phase-field code available. Continuous development by the OpenPhase Solutions team ensures that OpenPhase is state-of-the-art in simulating microstructure evolution.
Intuitive graphical user-interface
Guided creation of simulations, integrated documentation and presets for various materials and processes.
Modular library
OpenPhase Studio and OpenPhase Core use a modular structure that allows combining different physical modules into a single simulation or simulate a complex process through consecutive simulation steps.
Powerful diffusion module
Realistic simulation of diffusion and phase transformation. Coupling to Thermo-Calc and Open Calphad enables realistic simulation of complex material systems.
Extensive mechanics module
Finite strain elasticity snd crystal plasticity for complex mechanics simulations of evolving or static microstructures.
Straightforward flow solver
Fluid-flow solver using Lattice Boltzmann method for calculating melt flow during solidification.
Flexible nucleation and microstructure creation
Easy creation of initial microstructures, realistic nucleation based on various properties.
Meet Our Expert Team
Our team consists of leading experts in computational materials science, bringing together decades of experience in phase-field modeling and scientific software development.
Have Questions?
Find comprehensive answers to common questions about OPStudio, phase-field simulations, and our services in our detailed FAQ section.
Visit Our FAQ